Versatility And Customization Of Wire Harnesses
- Share
- publisher
- John
- Issue Time
- Feb 21,2025
Summary
As the core component of connecting modern equipment, the role of wire harness is not limited to simple electrical connections, but also to ensure the safe and reliable operation of equipment
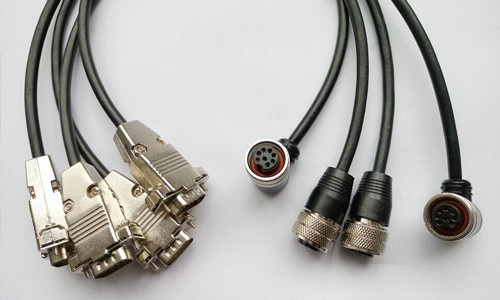
With the continuous improvement of industrial automation around the world, the application of large-scale production equipment has made the production of standardized wire harnesses more efficient and economical. Pipe standardized off-the-shelf wiring harnesses can meet general needs, but cannot meet connection needs in the face of increasingly complex operating conditions and environments. In the field of industrial automation, the diversification of equipment installation requirements has led to the increasing demand for customization and non-standard wiring harness installation.
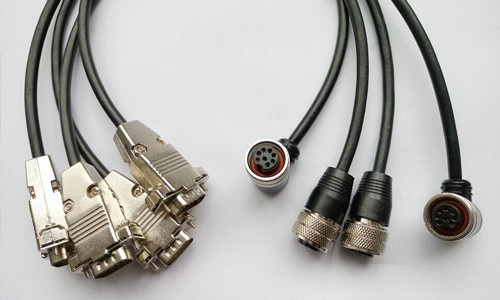
Background and significance of harness diversity
As the core component of connecting modern equipment, the role of wire harness is not limited to simple electrical connections, but also to ensure the safe and reliable operation of equipment. With the advancement of technology and the expansion of application fields, the design and manufacture of wire harnesses are facing higher requirements. For example, in new energy vehicles, the wiring harness not only has to undertake traditional signal transmission tasks, but also needs to support high-voltage power transmission, which presents a new challenge to the material selection and structural design of the wiring harness.
Necessity of wiring harness customization
In practical applications, different working conditions and environments put forward personalized requirements for wire harnesses. The necessity of wiring harness customization is analyzed from several dimensions as follows:
Segment demand
A single wire harness cannot meet the installation requirements of the whole system, and it is necessary to realize the functional partition through intermediate switching. Segment requirements involve not only protection requirements, but also factors such as installation dimensions. For example, when a long line has both motion and fixed demand, the cost will increase significantly if all tow chain wires are used. By adding a transfer point in the middle, and using a wire suitable for motion and fixed respectively, the cost can be effectively reduced.
Combined demand
With the improvement of system integration, the combination of multiple motor lines and coding lines has become a common demand. Integrating these lines into a single plug not only simplifies the installation process, but also improves signal transmission efficiency. The application of composite wire technology allows multiple motor wires or encoder wires to be made into a single cable, further reducing the wiring complexity.
Protection requirement
In industrial environments, wiring harnesses may face many challenges such as oil resistance, dust resistance, water resistance, and high temperature resistance. In order to meet these special needs, the protective properties of the wire harness can be enhanced by external application of plastic bellows, metal bellows or glass fiber tubes. Requirements for higher levels of protection, such as IP67 protection, can also be achieved through the joint injection molding process.
A practical case of wire harness customization
In order to better meet the individual needs of our customers, Connoder delves into their needs and offers a range of customization options for different scenarios:
Section wire selection
Provide fixed, tow chain, PVC, PUR and other materials of wire, users can choose the most suitable material according to the specific application scenario. At the same time, it also supports a variety of types of adapter plugs, including low cost but poor protection plastic plug-in type, better protection metal type and IP67 protection level of high-end plugs.
Custom specification
According to the specific needs of customers, any number of cores, wire diameters, lengths and colors of wire harnesses can be customized to match the requirements of complete installation. Fast matching connector solutions are also provided to ensure a balance between cost, delivery time and quality.
Protective measure
For special needs such as wear resistance, oil, water vapor, corrosion, debris and high temperature, different bellows can be selected for protection. This customized protection scheme not only improves the service life of the harness, but also guarantees the safe operation of the equipment.
The future trend of wire harness customization
Looking ahead, wiring harness customization will continue to evolve in a more intelligent and personalized direction. On the one hand, with the popularization of Internet of Things (IoT) and artificial intelligence (AI) technologies, wire harnesses will not only be a physical connection tool, but also become an important node for data acquisition and analysis. On the other hand, the development and application of new materials will further improve the performance of wire harnesses, enabling them to adapt to more extreme working environments.
The application of modular design methods will also promote the flexibility and efficiency of wire harness production. By establishing a database containing information such as connectors, terminals, wires, etc., Oems can more easily design and assemble wiring harnesses, thereby reducing development costs and shortening time to market.
The diversity and customization of wiring harnesses are the inevitable trend of modern industrial development. Only continuous innovation and technological progress can truly meet the increasingly complex industrial needs and promote the continuous development of the industry.