Tips and maintenance guide for industrial forklift connectors
- Share
- publisher
- John
- Issue Time
- Jan 2,2025
Summary
In the material handling and logistics industry, the industrial forklift connector is one of the key components, and its performance directly affects the efficiency and safety of the entire system.
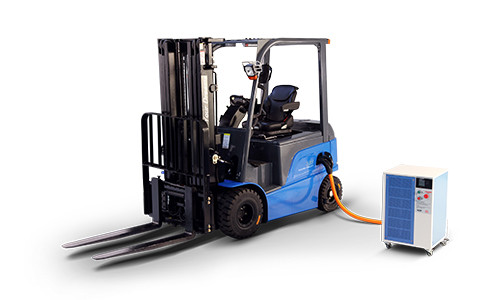
In the modern material handling and logistics industry, the industrial forklift connector is one of the key components, and its performance directly affects the efficiency and safety of the entire system. In order to ensure that the forklift connector can run efficiently for a long time and maximize its service life, this article will introduce a series of practical and effective use skills and maintenance strategies from a professional perspective.
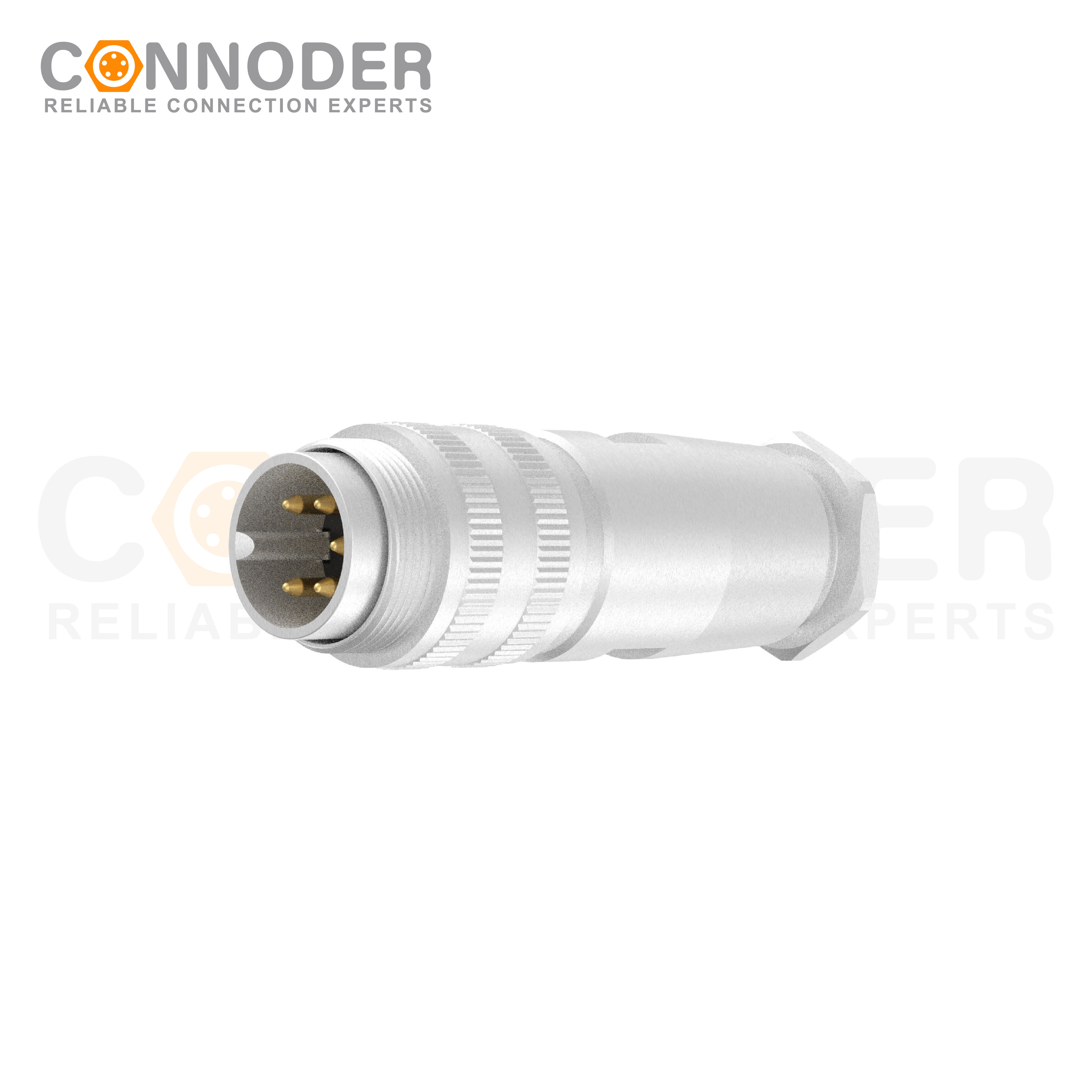

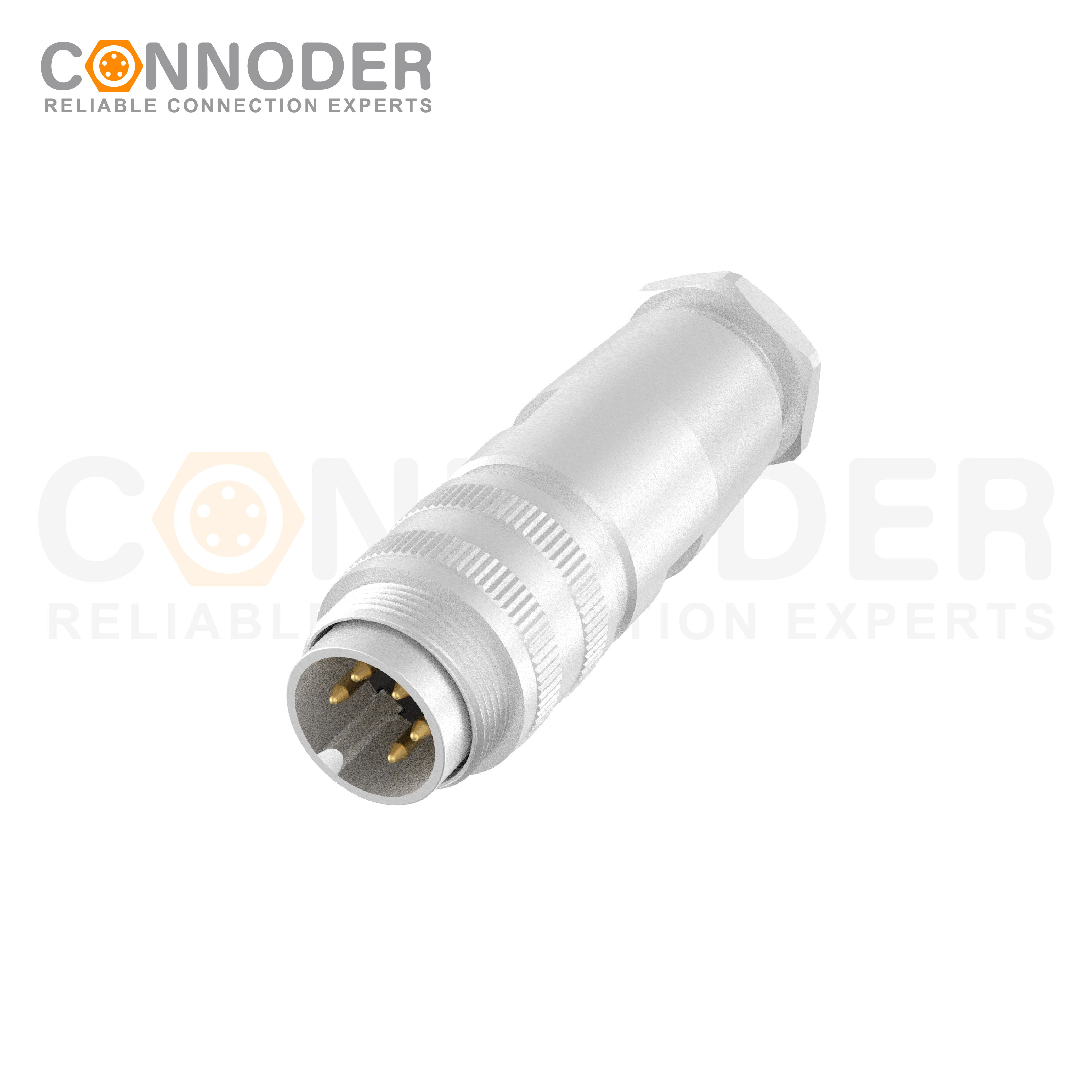
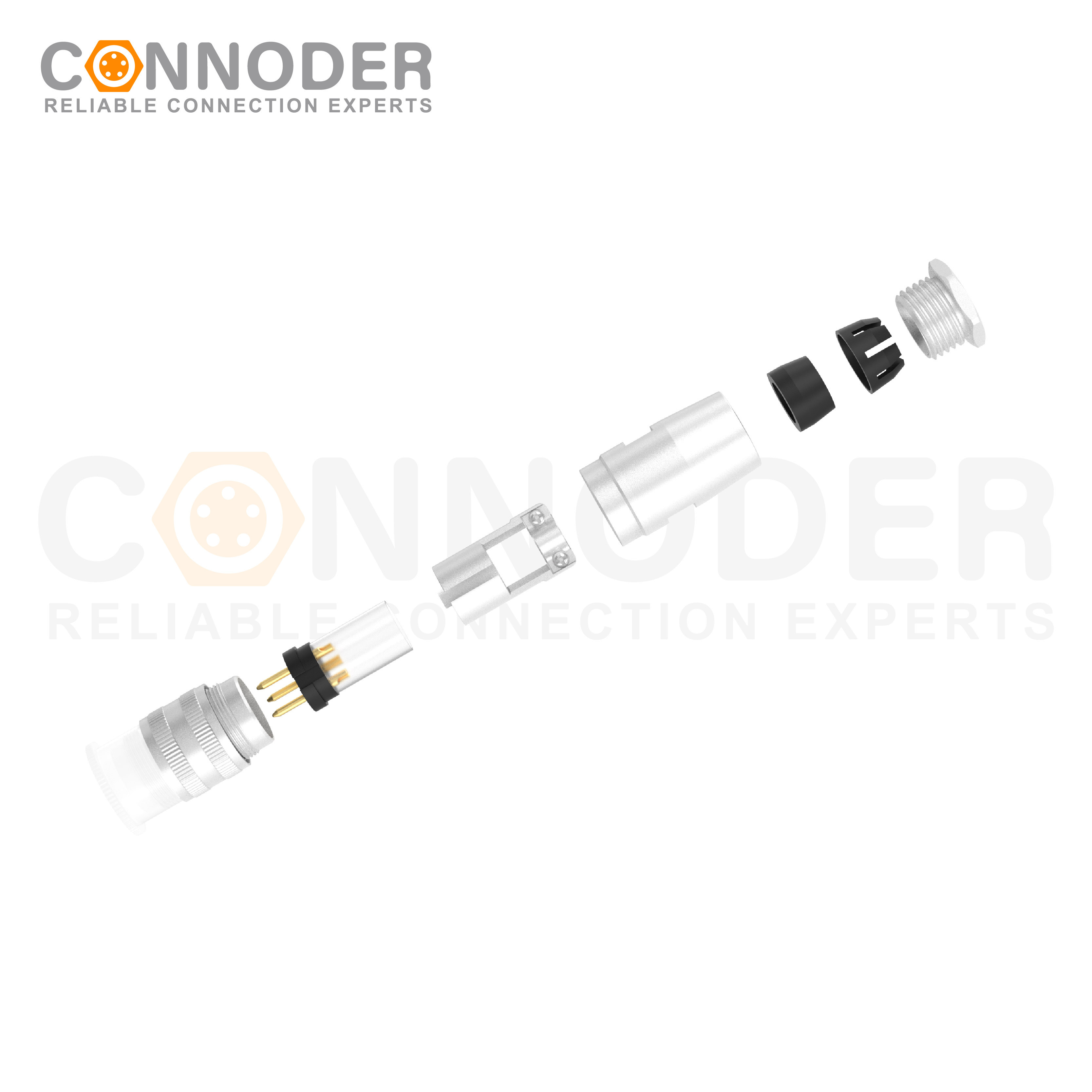
Regular inspection and maintenance of hydraulic system
For forklift connectors equipped with hydraulic systems, the state of hydraulic oil is one of the core factors to ensure the normal operation of the equipment. Therefore, it is necessary to establish a sound hydraulic system inspection system, including but not limited to the following:
Hydraulic oil level monitoring: regularly check whether the hydraulic oil level is within the specified range to avoid abnormal or damaged system pressure due to insufficient oil.
Hydraulic oil quality assessment: In addition to paying attention to the amount of oil, samples should be regularly taken to test the cleanliness and physical and chemical properties of hydraulic oil, and possible pollution problems should be found and dealt with in time.
Leak point investigation: Careful inspection of all joints, seals and other leakage prone locations, once found to take immediate repair measures to prevent small hidden dangers into major accidents.
Timely replacement of worn parts
Any mechanical equipment will naturally wear over time, and forklift connectors are no exception. Ignoring these subtle changes, however, could have major security implications. Therefore, when the following situations are found, the relevant parts should not hesitate to replace:
Surface damage: Such as cracks, dents, or other forms of physical damage, this may be due to material fatigue or external impact.
Functional abnormalities: such as not close enough connection, slow movement and other problems, often imply that the internal structure has been affected to a certain extent.
Beyond service life: Even if there are no obvious signs of failure, active replacement is recommended as long as the maximum service life recommended by the manufacturer is reached to reduce potential risks.
Reasonable storage and proper storage
The correct storage method can not only protect forklift connectors from the external environment, but also effectively delay the aging process. Specific practices are as follows:
Dry environment: Store in a place with good ventilation and low humidity to prevent rust and corrosion of metal parts.
Dust prevention measures: By covering the special protective cover and other ways to reduce dust accumulation, keep the appearance clean and tidy.
Temperature control: Try to avoid long-term exposure to extreme hot and cold conditions, so as not to cause material characteristics to change.
Professional training of operators
No matter how advanced the equipment, ultimately need to rely on people to operate to maximize effectiveness. Therefore, it is particularly important to strengthen staff skills training:
Theoretical study: Organize regular lectures or seminars to explain in depth the working principle and importance of forklift connectors.
Practical exercise: Provide ample opportunities for each participant to practice and familiarize themselves with various operational processes.
Safety awareness training: emphasize the importance of compliance with rules and regulations, and establish the idea of "prevention first".
Development and implementation of maintenance plans
Scientific and reasonable maintenance plan is the basis of long-term management. It should cover the following areas:
Periodic arrangement: Determine the inspection interval of different items according to the actual frequency of use, and form a fixed schedule.
Division of responsibilities: Define the specific person responsible for each task and its scope of responsibility to ensure that it is implemented in place.
Record and archive: Record the contents and results of each maintenance activity in detail for subsequent analysis and reference.
In addition, it can also use modern information technology means (such as the Internet of Things remote monitoring platform) to achieve intelligent management, further improve work efficiency and service level.