Design and application of wire harness
- Share
- publisher
- John
- Issue Time
- Feb 19,2025
Summary
As an indispensable part of modern industrial equipment, the design and application of industrial wire harness directly affect the performance, reliability and cost of the whole system.
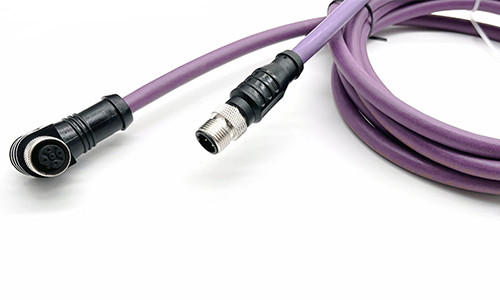
As an indispensable part of modern industrial equipment, the design and application of industrial wire harness directly affect the performance, reliability and cost of the whole system. With the improvement of industrial automation and the development of intelligent trend, the design of industrial wire harnesses becomes more and more complex and important. Starting from the basic concept of wire harness, this paper will deeply discuss the design principles, technical requirements, manufacturing process and wide application in different fields of industrial wire harness.
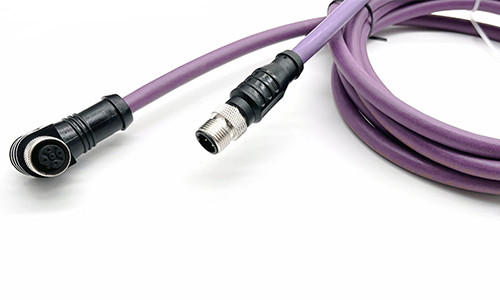
Cognitive harness
Wire harnesses are external coats or sheathing that protect internal conductors or bundles of conductors that may already have sheathing for insulation and protection, or they may rely on wire harnesses to create an ideal working environment. The core role of wiring harnesses is to provide key organizational functions and to achieve them through simple, straightforward, low-cost design. Although many professionals often use cable assemblies and harnesses interchangeably, the two can actually be differentiated according to specific needs to adapt to different environments and application scenarios.
Design principles of industrial wire harnesses
Safety: The primary consideration in the design of industrial wiring harnesses is safety, which must ensure that the wiring harnesses can withstand temperature changes, vibration and other physical stresses in the working environment.
Electromagnetic Compatibility (EMC) : Proper shielding and grounding measures are essential to reduce the impact of external interference on signal transmission, while preventing itself from becoming a source of interference. This is particularly important in areas such as aerospace and medical care.
Modular design: Dividing different functions into separate modules can simplify production and maintenance processes, while increasing the flexibility of the design so that it can quickly respond to changes in market requirements.
Technical requirements for industrial wiring harnesses
In order to meet the requirements of specific industrial environments, industrial wiring harnesses must meet certain technical standards. This includes, but is not limited to, the selection of wire specifications, the establishment of connector types, and the setting of protection levels. For example, for high-current carrying systems that require long-term stable operation, such as industrial power supplies, the wiring harness not only needs to be flexible enough for easy installation and adjustment, but also needs to achieve IP67 or higher protection levels.
Manufacturing process of industrial wire harness
The production of industrial wire harnesses involves multiple links, from raw material procurement to final product inspection, and each step requires strict quality control. It is particularly important to use error prevention technology in the wiring harness manufacturing process, such as process error prevention design and tooling error prevention design to avoid possible errors, so as to improve product consistency and reliability. In addition, three-dimensional simulation using advanced CAD software can help engineers better plan the path of the wire harness, maximize space utilization while reducing material consumption.
Application scenarios of industrial wiring harnesses
Industrial wiring harnesses are widely used in various types of mechanical equipment, including office equipment (such as printers, copiers), industrial control devices (such as inspection equipment), and many other fields. For example, in the aerospace field, cable assemblies are widely used in drones, satellites and aircraft to promote the transmission of electricity, communications, etc. In the automotive industry, electrical wiring harnesses are critical to saving valuable space while helping to organize complex wiring.
Other typical applications include:
Medical industry: Hospitals and clinics rely on wire harnesses to organize and protect wires inside equipment, including emergency vehicles, diagnostic and imaging equipment, dental equipment, and more.
Telecommunications industry: Wiring harnesses optimize the space utilization of various telecommunications equipment such as modems, routers, Repeaters, etc.
Information Technology: Almost all computers, laptops, servers, and other information technology devices contain wiring harnesses to optimize space and organize wires.
Construction industry: Wire harnesses are widely used in structures to provide wire insulation and organization.
Manufacturing: CNC machine tools and other power manufacturing equipment rely on wire harnesses to guide and organize internal and external wires.
Robotics and Automation: Wiring harnesses are widely used in most automation devices and robots to securely route, group, and protect critical lines.
Advantages of industrial wiring harnesses
Industrial wiring harnesses offer significant benefits, including reduced costs, improved organization, reduced installation time, protection of conductors from environmental impacts, safer working environments, and enhanced safety. For example, by organizing loose or scattered wires, wiring harnesses can maximize space and prevent tripping and damage to wires and cables. In addition, the choice of high-quality insulating materials such as PVC, polyethylene, polyurethane, etc. is crucial to ensure the durability and reliability of the wiring harness.
Selection of high performance materials
Choosing the right high-performance material for your specific needs is critical to ensuring optimal performance for your harness. For example, in environments with high humidity, it may be necessary to use waterproof materials such as polyethylene to avoid damage to conductors. Connoder offers custom wiring harness services that can be customized to virtually any specification to meet the specific needs of multiple industries such as aerospace, automotive, medical, telecommunications, and more.
To sum up, the design and application of industrial wiring harness is a highly comprehensive technical field, involving mechanical engineering, electronic engineering and other disciplines. With the progress of science and technology and the development of society, the future industrial wiring harness will move towards a more intelligent and integrated direction.